Braking
Find your replacement part
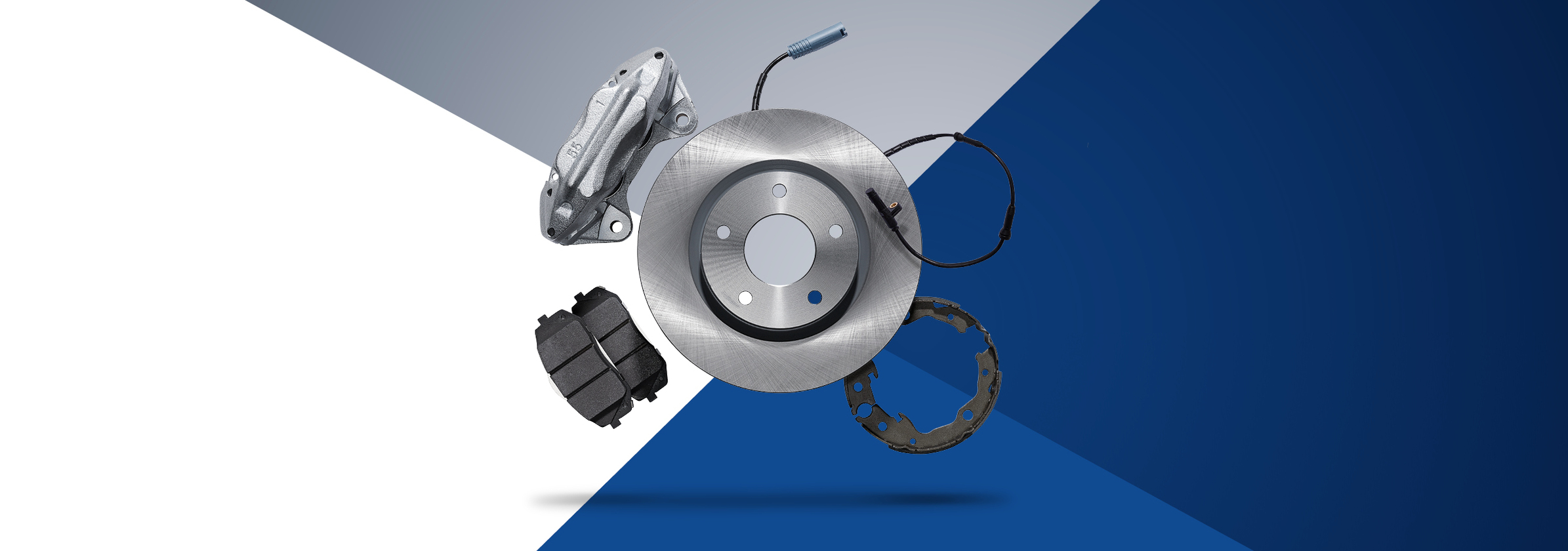
Why Blue Print Braking?
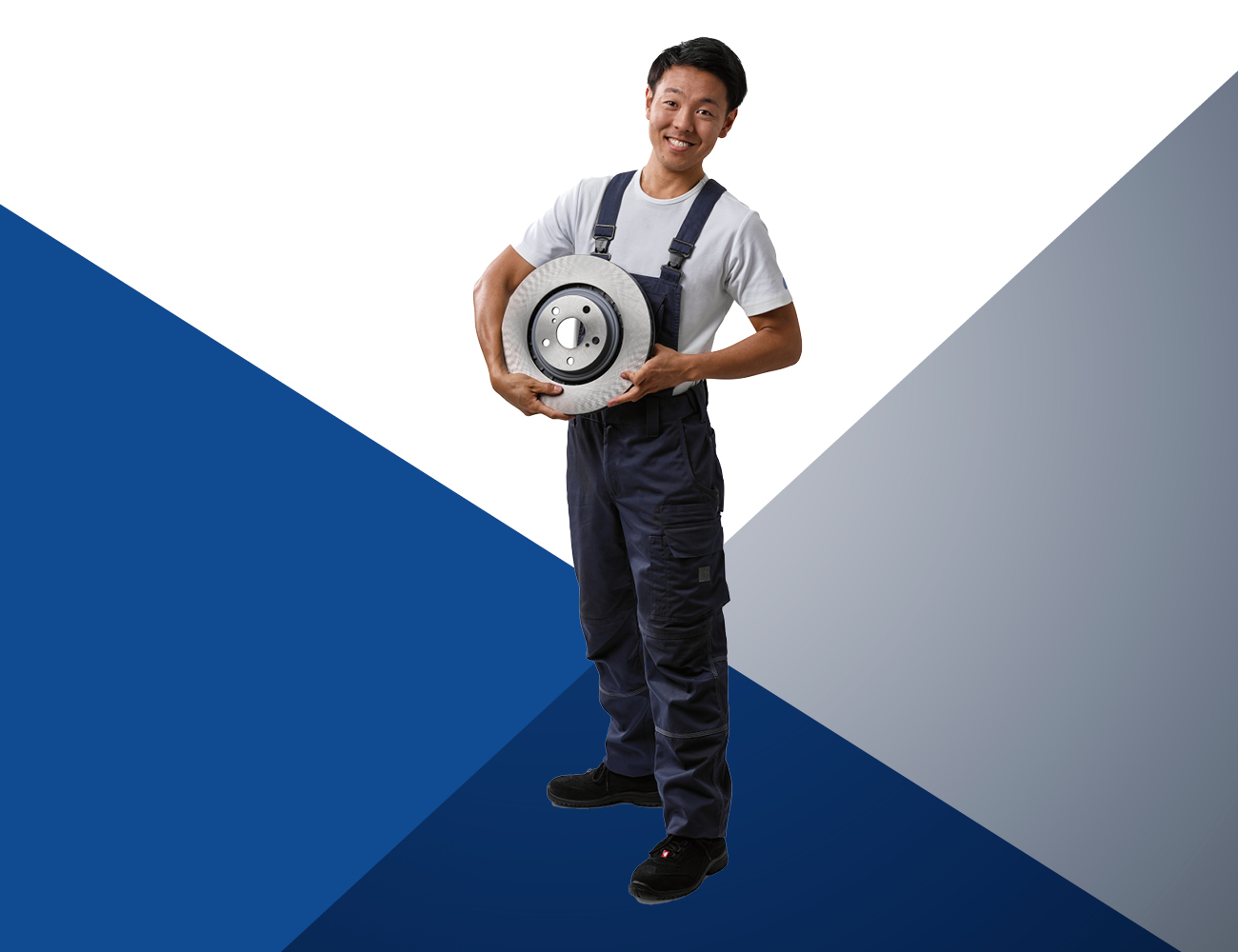
Brake Discs
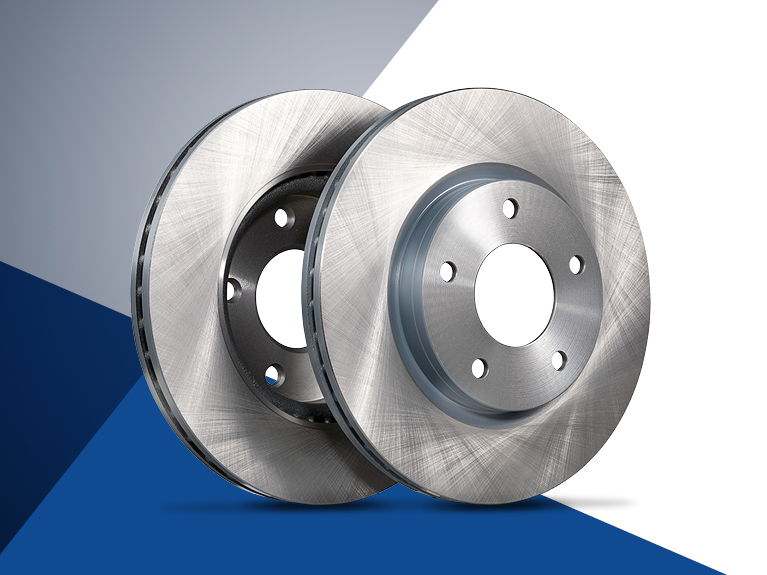
The Heat is On
As the brake disc rotates with the wheel, it is clamped by the brake pad friction material with pressure from the piston(s) to decelerate the disc rotation, which slows and eventually stops the vehicle. This action creates a lot of thermal energy, which produces a level of heat dependant on the speed and weight of the vehicle and how hard the brakes are pressed.
Heat can cause the brakes to become less effective and fade due to prolonged and/or ‘heavy’ braking. Overheated discs can suffer from excessive wear and potential break-up, the driver may have to press harder on the brake pedal to slow the vehicle down and, in extreme cases, the brakes may get so hot that they cannot generate enough friction regardless of how hard the pedal is pressed.
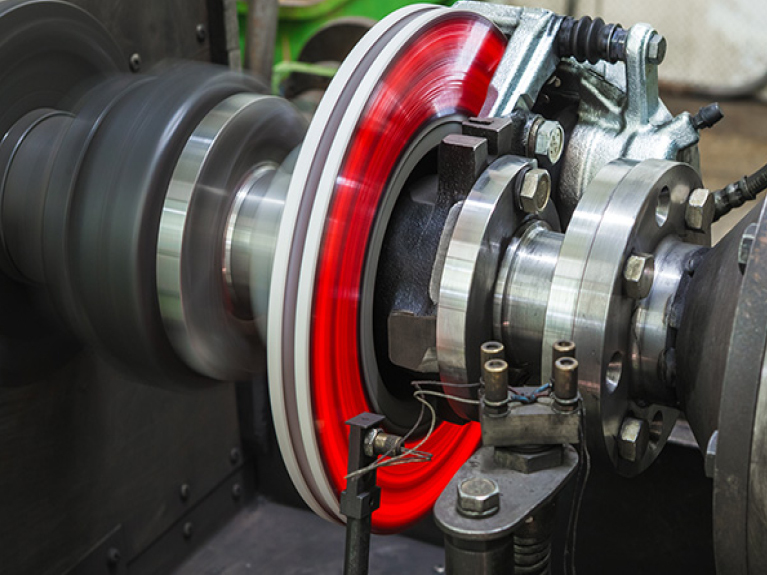
However, as main components are exposed to the atmosphere, this heat can be diffused efficiently, thus reducing brake fade.
The construction of the brake disc is important for safety reasons - it must have the ability to dissipate heat quickly, effectively and in the right areas. Therefore, the disc must be the right weight, mass and thickness, and be made of the necessary material including a high carbon composition.
Blue Print has a wide range of over 1,750 brake discs, covering more than 96% of all common Asian and European vehicles from the year 2000 onward.
From Raw Materials to Precision Product
Blue Print brake discs are manufactured to the highest standards using a grey-iron smelting process consisting of new and recycled materials combining metal composites. Choosing the right material is critical to the quality and operation of the brake discs for each vehicle application.
Multiple cast-iron chemical compositions are used, enriched with alloy components to enhance tensile strength and hardness for optimal performance. Such components include molybdenum, copper, chrome and titanium.

Brake Discs with Integrated Wheel Bearings
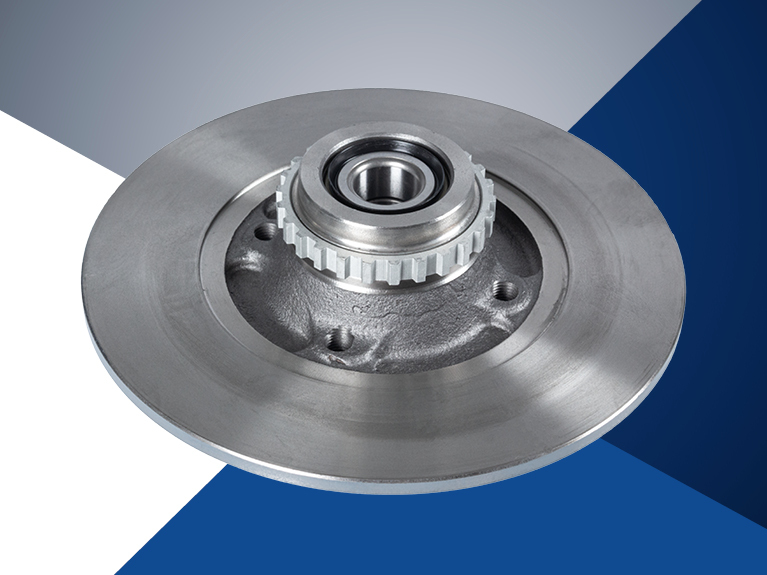
Some vehicles - particularly Renault, Peugeot and Citroën models - use brake discs with an integrated wheel bearing on the rear axle.
This assembly type, established by the vehicle manufacturer, results in significant weight savings since the brake disc also becomes the wheel hub. This disc/bearing assembly is equipped with a phonic wheel - a magnetic encoder for the wheel speed sensor to establish acceleration and deceleration to monitor wheel speed. The wheel speed signal is transposed by the vehicle’s control units and used for the operation of ABS and other stability-control functions.
This preassembled part makes replacement easier and quicker for the workshop, ensuring a perfect fit and eliminating the risk of mounting a bearing with incorrect clearance or seal positioning. This is essential for a safety component’s operation and security.
Brake Pads
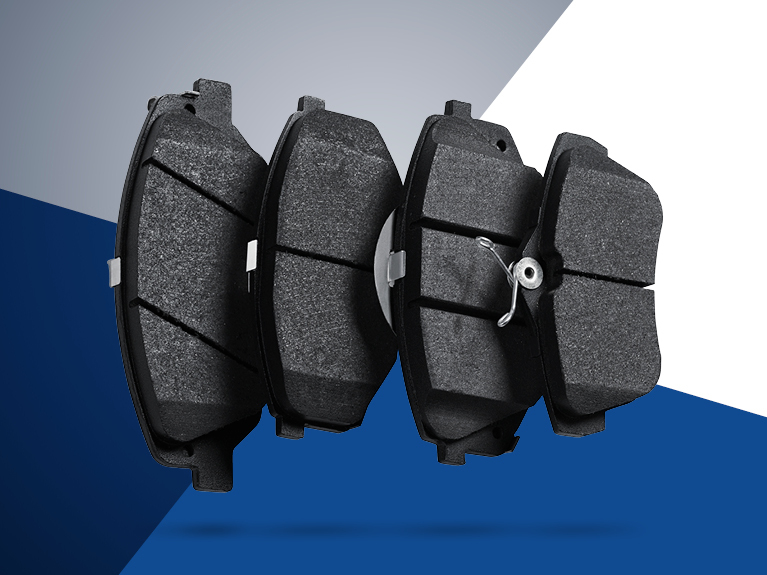
Blue Print aims to find the optimal solution for safety, comfort and efficiency for every brake pad. Each brake pad set, of which there are more than 1,330 in range for Asian and European vehicles, features high shear strength, excellent stability-friction coefficient, low noise levels and minimum vibration - providing a secure feeling for the driver as braking is more progressive and comfortable.
A decisive factor for optimal brake pad quality is the individual components which form each pad. Combining these elements provides reliability and safety.
Friction Material: Specifically matched to a particular vehicle type and model.
Intermediate Layer: Optimised compressibility reduces heat transfer.
Adhesive: High shear strength; bonds friction material to the pad carrier.
Backing Plate: High material strength.
Shim: Reduces brake noise and fitted to the steel backing plate to dampen vibrations between the pad and caliper
Brake Drums & Shoes
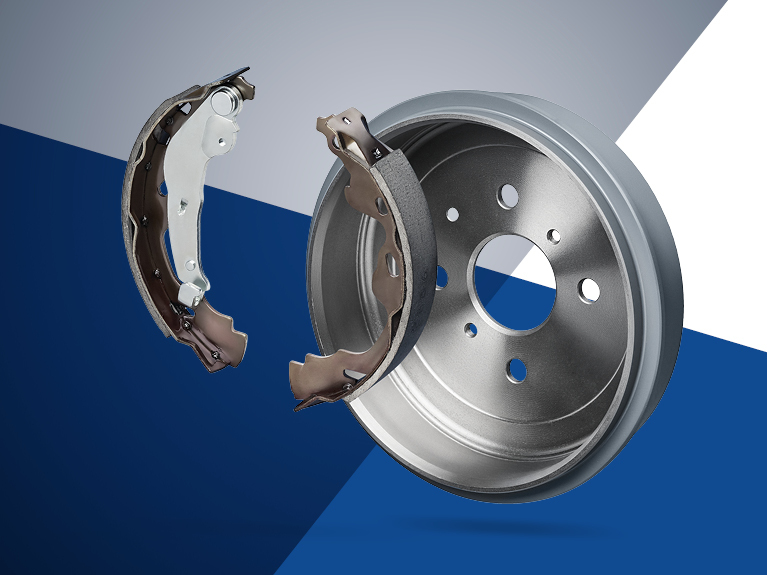
Drum brakes are typically used in the rear-braking system of smaller cars, but they can also serve as a parking brake.
When the brake pedal is applied, the wheel-cylinder pistons press against the brake shoes and force them outwards. As a result, the friction that is generated from the brake linings - against the inner surface of the drum - decelerates and stops the vehicle.
Blue Print has an excellent range of more than 130 brake drums and 300 brake shoes, covering more than 14,800 Asian and European vehicles.
Leading or Trailing
There are three types of drum brake design subject to how the brake shoes are pressed onto the drums: leading/trailing, twin-leading and duo-servo.
Today, the most common type used on passenger cars is leading/trailing. The ‘leading shoe’ features a shoe that moves in the direction of rotation when it is being pressed against the drum, and the ‘trailing shoe’ is pressed in the same direction as the rotation of the drums, helping to push the shoes against the drum with greater pressure for a stronger braking force. This is the ‘servo effect’, which supplies the braking force to drum brakes in order to decelerate and stop rotation.
Brakes for All Makes.
Brakes for All LCVs!
The countless braking manoeuvres performed by LCVs during a typical busy day result in faster wear and tear on all braking components than compared to a normal car. With its All-Makes range, Blue Print are proud to offer over 890 braking components for popular Asian and European LCVs on Europe's roads.
When it comes to braking, we have the right replacement part, whatever your LCV may be!
Discover Blue Print for LCVs
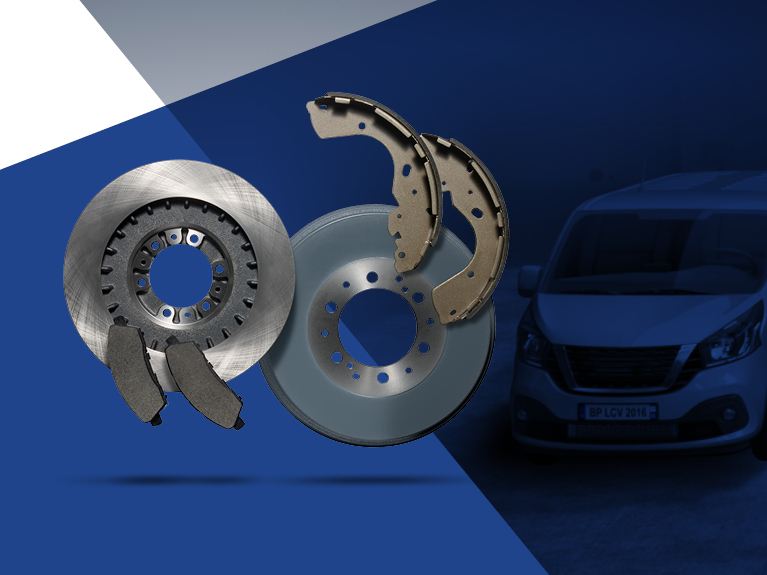